The Evolution of Robotics in Industry
From Manufacturing to Service Sectors
- Robotics initially found widespread use in manufacturing industries, particularly in automobile assembly lines where precision, speed, and consistency were paramount.
- Companies like General Motors and Toyota utilized robotic arms to perform welding, painting, and assembly tasks, enhancing productivity and reducing human error.
- Over time, the adoption of robotics expanded to other industries. In the healthcare sector, robots assist in surgeries, deliver medications, and manage inventory.
- Service sectors like hospitality and retail also leverage robotic technologies. For instance, hotels use robots for room service deliveries, while retail stores employ them for inventory management and customer interactions.
- Robotics continues to penetrate various service-oriented sectors, broadening its impact beyond traditional manufacturing roles.
This evolution signifies the technology’s adaptability and potential to revolutionize diverse work environments.
Technological Breakthroughs Driving Change
Technological advancements have been pivotal in evolving industrial robotics.
The development of artificial intelligence (AI) and machine learning enhances robots’ ability to perform complex tasks.
AI enables robots to learn and adapt to new situations, improving their efficiency and functionality.
The introduction of collaborative robots, or cobots, has transformed workplace dynamics.
Unlike traditional industrial robots that operate in isolated environments, cobots work alongside human employees, assisting with tasks that require precision and repetitive actions.
According to the International Federation of Robotics, the sales of cobots increased by 11% in 2020, reflecting their growing popularity.
Breakthroughs in sensor technology and computer vision systems have further augmented robotic capabilities.
High-resolution cameras and advanced sensors enable robots to perceive their surroundings accurately, enhancing their performance in tasks like quality inspection and sorting.
3D printing technology and advancements in materials science also contribute to the evolution of robotics.
Lightweight materials and sophisticated manufacturing processes allow the creation of more efficient, durable robots with a broader range of applications.
The evolution of robotics in industry is marked by significant technological advancements and a shift from manufacturing-centric roles to diverse service sector applications.
This dynamic progression highlights the transformative potential of robotics across various industries globally.
Impact of Automation on Employment
Job Creation Through Advanced Robotics
Automation brings job creation benefits, particularly through the development and maintenance of robotic systems.
Jobs in engineering, software development, and data analysis have seen an uptick as companies incorporate more advanced robotics.
In manufacturing, for instance, skilled technicians are needed to oversee robotic production lines, ensuring machines function correctly.
Moreover, roles in AI and machine learning have expanded significantly.
Professionals in these fields work on enhancing robotic capabilities, making them more efficient and adaptable.
The healthcare sector also benefits, with new positions in robotic-assisted surgery and patient care.
In retail, roles focus on integrating robotic systems to streamline inventory management and customer service.
Challenges of Job Displacement
Automation does present challenges, the most significant being job displacement. Lower-skilled positions are most at risk as companies automate repetitive tasks.
For example, assembly line workers may find their roles automated by robotic arms capable of working faster and more precisely.
In the service industry, cashiers and clerks face displacement due to self-checkout systems and automated customer service bots.
However, there is a growing need for workers skilled in technology maintenance and programming.
The transitional phase requires governments and organizations to invest in reskilling initiatives to prepare the workforce for new technological demands.
Robotics and Workplace Safety
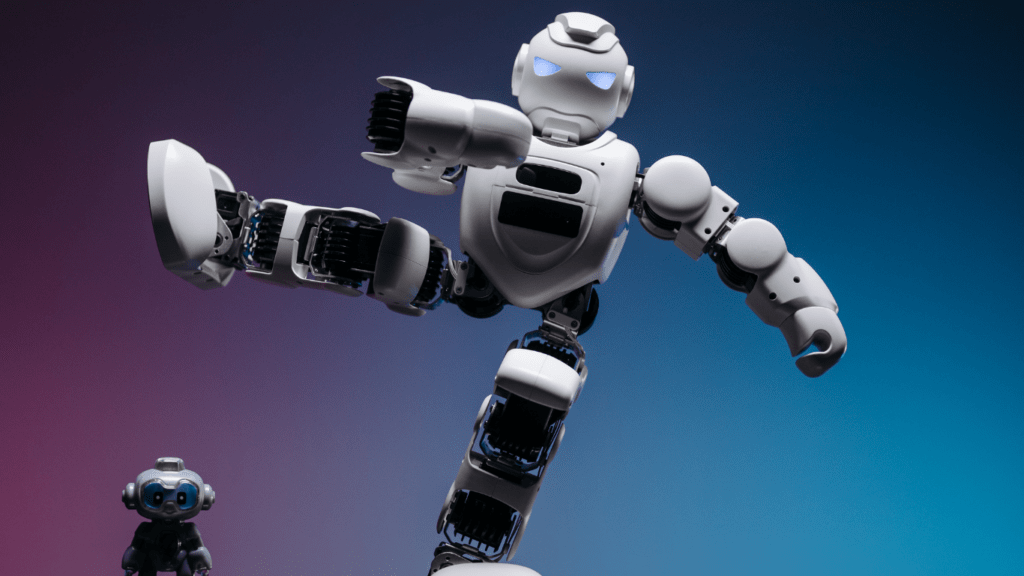
Enhancing Worker Safety with Robotics
Robotics improves workplace safety by taking over hazardous tasks.
For example, robots can handle toxic substances, reducing workers’ exposure to harmful chemicals.
They can also perform repetitive tasks that cause strain injuries, such as lifting heavy materials.
By automating these roles, companies reduce workplace injuries and ensure a safer environment for employees.
According to the Occupational Safety and Health Administration (OSHA), using robots results in fewer workplace injuries and fatalities.
Challenges of Implementing Safety Protocols
Integrating robotics involves ensuring the safety of human workers and machinery.
Developing effective safety protocols can be complex due to the need for precision. Robots and humans need to work in close proximity; hence, collision-avoidance systems must function flawlessly.
Moreover, regulatory compliance, such as OSHA rules, adds another layer of complexity.
The International Federation of Robotics (IFR) states that many companies face challenges in training workers to operate alongside robots safely, adding another obstacle to seamless implementation.
Future Trends in Industrial Robotics
Predicting the Next Decade
Future trends in industrial robotics point towards significant advancements and widespread adoption.
According to the International Federation of Robotics, the number of industrial robots globally is expected to surpass 3.7 million units by 2025.
Industries like:
- automotive
- electronics
- logistics
will drive this growth.
Advances in sensor technology will enhance robots’ precision, allowing them to handle more complex tasks.
Developments in collaborative robots (cobots) will revolutionize workplaces by working alongside humans safely and efficiently. Cost reductions in robotic technologies will make automation accessible to smaller businesses, not just large corporations.
Integration with Artificial Intelligence
Artificial Intelligence (AI) will play a crucial role in transforming industrial robotics. Machine learning algorithms will enable robots to learn from data, improving their decision-making capabilities.
AI-driven robotics will handle tasks requiring adaptability, such as quality inspection and predictive maintenance.
Natural language processing will allow users to interact with robots more intuitively, reducing the need for specialized programming knowledge.
The combination of AI and robotics will lead to smarter factories, where systems can optimize production processes, reduce downtime, and increase overall efficiency.
By focusing on these future trends, industries can prepare for the transformative impact of advanced robotics, driving growth and innovation.